La qualità dei prodotti è la chiave del successo competitivo di ogni produttore sul mercato. Pertanto, ogni produttore si concentra sulla qualità dei prodotti e dei servizi. I produttori che non si rendono conto dell'importanza di questo aspetto si perdono sulla strada del successo. La qualità è una delle caratteristiche più essenziali per un marchio per dominare il mercato, guadagnando la fiducia dei clienti e rendendo il marchio più affidabile rispetto ai concorrenti. Pertanto, il mantenimento di standard di qualità per i prodotti fisici e i servizi post-vendita è il fattore più cruciale per ogni produttore. In questo caso, il PPAP è uno degli standard di qualità dei prodotti essenziali nella maggior parte delle industrie manifatturiere.
Questo articolo introduce il processo di approvazione dei pezzi di produzione o PPAP. Verrà inoltre sottolineata l'importanza del PPAP per le prestazioni del prodotto sul mercato. Verranno inoltre evidenziati i cinque livelli PPAP, che svolgono un ruolo significativo nella produzione. Alla fine dell'articolo, discuteremo alcuni degli elementi essenziali del PPAP e delle aziende che applicano gli standard PPAP.
Che cos'è il processo di approvazione dei pezzi di produzione o PPAP?
Come suggerisce il titolo della sezione, PPAP è l'acronimo di Production Part Approval Process (processo di approvazione dei pezzi di produzione), un acronimo tipico della produzione. Il PPAP è la chiave per una produzione coerente di parti e componenti nell'industria automobilistica. Comprende 18 elementi. Questo processo completo garantisce la produzione di alta qualità di componenti e attrezzature che i consumatori si aspettano.
L'origine dello standard PPAP è l'industria aerospaziale e automobilistica. In particolare nell'AIAG o Automotive Industry Action Group. In seguito, questo standard si è diffuso in tutti gli altri stabilimenti produttivi per migliorare la qualità della produzione. Il PPAP supporta tutte le attività critiche dell'ingegneria di produzione e facilita la collaborazione tra fornitori e acquirenti. Anche questo processo fa parte dell'APQP. APQP è l'acronimo di pianificazione avanzata della qualità del prodotto.
Se un imprenditore avvia una catena di fornitura relativa al settore automobilistico, deve condurre il PPAP. Oltre alle catene di fornitura automobilistiche, anche altri settori praticano il PPAP per garantire i progetti e le specifiche ingegneristiche. In questo caso, le aziende responsabili, FCA US, Ford Motors e General Motors, hanno indicato il PPAP come esigenza specifica del cliente o CSR.
Importanza del PPAP
Il PPAP è fondamentale. Garantisce che il pezzo prodotto richiesto per le specifiche di un'automobile o di un macchinario sia corretto come previsto. Fornisce una linea guida semplice che consente ai fornitori di migliorare la comunicazione. Ogni ciclo di produzione in una fabbrica consente di ottenere la qualità e la garanzia del prodotto richiesto attraverso il PPAP. Di conseguenza, riduce i rischi e migliora l'attuazione delle azioni corrette. Il PPAP rende più fluido il processo di produzione. Tuttavia, i tre punti seguenti sono lo scopo principale del PPAP.
- Garantire che il fornitore mantenga i requisiti di qualità del prodotto del cliente.
- Dimostrare che il produttore o il fornitore ha soddisfatto tutte le specifiche del prodotto e i requisiti dei disegni ingegneristici
- Per verificare il processo di produzione approvato
Quali sono i cinque livelli di PPAP?
I cinque livelli di PPAP sono noti come i cinque livelli di presentazione delle parti. Questi cinque livelli di presentazione delle parti sono fondamentali per il processo PPAP e il cliente deve ottenere questi documenti dal venditore. In questo caso, quando un cliente richiede il PPAP, seguirà questo livello di presentazione delle parti.
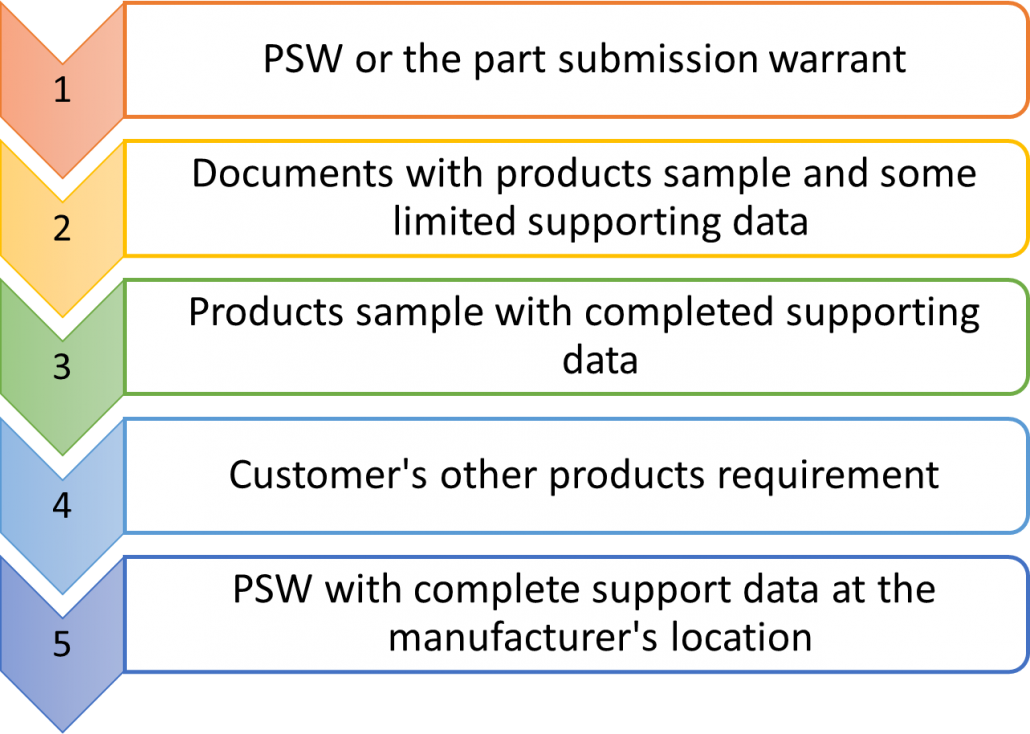
Secondo l'AIAG (Automotive Industry Action Group), il venditore deve considerare gli elementi essenziali del PPAP di un pezzo fabbricato. Tuttavia, la presentazione dei dettagli necessari dipende dal pezzo e dai requisiti dell'ordine di acquisto. I cinque livelli PPAP indicano i documenti che il fornitore deve consegnare al cliente.
- PSW o il mandato di presentazione parziale (livello 1)
- Documenti con campioni di prodotto e alcuni dati di supporto limitati (Livello 2)
- Campione di prodotto con dati di supporto completi (Livello 3)
- Esigenze di altri prodotti del cliente (livello 4)
- PSW con dati di supporto completi presso la sede del produttore. (Livello 5)
Il PSW o garanzia di presentazione del pezzo fa parte del processo PPAP. Di solito indica la prova che il fornitore è in grado di soddisfare le richieste del cliente. Questi documenti includono la data di consegna, il tasso di produzione e la qualità del prodotto. Un fornitore deve garantire tutti questi elementi applicativi. D'altra parte, i controlli di qualità PSW prevedono un'adeguata verifica dei prodotti.
In base ai cinque livelli di PPAP sopra descritti, è essenziale notare che questi livelli sono a discrezione dell'acquirente. In questo caso, è necessario essere più specifici su quale situazione richiede quale livello PPAP. Pertanto, ogni fornitore deve conservare tutti questi dettagli dai produttori.
Elementi del processo di approvazione delle parti del prodotto nella produzione
L'AIAG ha fondato la lista di controllo PPAP e ha rilasciato di recente la versione 4. Secondo l'ultima versione del manuale PPAP, sono 18 i documenti principali richiesti per la produzione di componenti automobilistici. In questa sezione vi presenteremo brevemente questi 18 elementi.
- I documenti di progettazione comprendono i disegni dei clienti e dei fornitori, la composizione dei materiali e gli ordini di acquisto.
- I documenti per le modifiche ingegneristiche includono i dettagli sulle esigenze di modifica da parte del cliente e l'ECN o avviso di modifica ingegneristica da parte del dipartimento di ingegneria.
- La prova dell'approvazione ingegneristica comprende i rapporti di prova campione approvati dall'ufficio tecnico.
- Design FMEA: la DFMEA o Design Failure Mode and Effects Analysis comprende le modalità di guasto e i loro effetti sul pezzo.
- I diagrammi di flusso del processo descrivono l'intero processo di produzione e assemblaggio.
- FMEA di processo: la PFMEA o analisi delle modalità e degli effetti dei guasti di processo comprende tutti i possibili guasti della qualità del processo e i loro effetti sui prodotti finali.
- Il piano di controllo è la fase successiva della PFMEA.
- L'analisi del sistema di misura comprende la ripetibilità e la riproducibilità del calibro (GR&R).
- L'analisi dimensionale rappresenta i dati, compresa la tolleranza e altri fattori.
- I risultati dei test sulle prestazioni dei materiali includono un piano e un rapporto di verifica della progettazione (DVP&R).
- Gli studi iniziali sui processi comprendono il controllo statistico dei processi (SPC).
- La documentazione per i test di laboratorio qualificati comprende i certificati approvati da qualsiasi laboratorio di analisi di qualità.
- Il rapporto di approvazione dell'aspetto comprende i componenti che influiscono sull'aspetto del pezzo in prova.
- Prodotto campione.
- Campione di esperti: Questo campione proviene solitamente dal collaudo finale e dalle approvazioni del reparto tecnico del produttore.
- Gli ausili per il controllo comprendono strumenti per ispezionare, testare o misurare le parti durante il processo di assemblaggio.
- Rapporti di approvazione dei requisiti specifici del cliente.
- PSW o mandato di presentazione parziale, compresi i cinque livelli di presentazione.
PPAP vs APQP
Consideriamo innanzitutto l'abbreviazione di entrambi i termini. PPAP sta per Production Part Approval Process (processo di approvazione delle parti di produzione) e APQP sta per Advanced Production Quality Planning (pianificazione avanzata della qualità della produzione). Il PPAP si occupa dei requisiti di progettazione del prodotto e del design richiesto dal cliente, del processo e della progettazione FMEAA, del diagramma di flusso del processo, del piano di controllo, ecc.
D'altra parte, l'APQP si occupa della produzione complessiva e dello sviluppo dei processi. L'APQP ha cinque gate, tra cui i requisiti AIAG APQP. Ciascuna porta definisce i diversi documenti e requisiti. Le cinque fasi dell'APQP sono:
- Definizione del piano e del programma
- Verifica della progettazione e dello sviluppo del prodotto
- Verifica della progettazione e dello sviluppo del processo
- Convalida del prodotto e feedback
- Lancio, valutazione e correzione
È importante notare che il processo di approvazione dei pezzi di produzione deriva dall'APQP. Nel corso del processo APQP, verranno ulteriormente controllati i documenti PPAP. La fase APQP si occuperà anche della revisione tecnica e dell'approvazione degli utensili per i pezzi fuori produzione.
Chi è responsabile del PPAP e quando è necessario?
I fornitori o i produttori sono responsabili degli elementi PPAP. Preparano tutti i documenti PPAP necessari per ogni tipo di prodotto. I produttori di solito gestiscono il processo in stretta collaborazione con il team di gestione della qualità dell'OEM.
Un processo di approvazione dei pezzi di produzione è necessario per la produzione di nuovi pezzi, per le modifiche o le correzioni dimensionali del prodotto, per le modifiche o le correzioni di processo e per gli utensili inattivi da oltre un anno. In questo caso, la modifica del prodotto può includere il design, la composizione del materiale, la fornitura e la funzione. D'altra parte, la modifica del processo può consistere in un metodo, in strumenti, in un luogo e in criteri di ispezione.
Cos'è l'AIAG e cosa fa l'AIAG?
L'AIAG, o Automotive Industry Action Group, è un'associazione commerciale senza scopo di lucro i cui membri sono la maggior parte delle case automobilistiche, i fornitori di tutte le dimensioni, le case automobilistiche, ecc. In particolare, i membri dell'AIAG includono Ford, General Motors, Toyota, Honda, Nissan, Caterpillar e più di 800 OEM. Tuttavia, il PPAP è uno degli standard più validi che hanno avuto origine dall'AIAG.
Il ruolo principale dell'AIAG è quello di fornire un forum aperto e neutrale per facilitare le azioni di produzione e le questioni comuni. L'obiettivo è sviluppare standard e linee guida per i processi aziendali. Educano e formano le persone attraverso valutazioni, eventi e newsletter per creare una catena di fornitura più efficiente e responsabile.
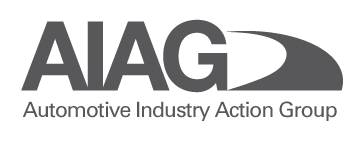
Conclusione
Il PPAP è necessario non solo per la qualità del processo produttivo, ma anche per mantenere una fornitura di alta qualità. Il processo di approvazione dei pezzi di produzione è la chiave della maggior parte delle industrie automobilistiche. Anche la produzione di nastri di tenuta richiede il PPAP, poiché il tipo di nastro di tenuta comprende parti automobilistiche. Esistono cinque livelli di PPAP, in cui il PSW o garanzia di presentazione del pezzo è l'elemento essenziale.
Il più recente manuale PPAP afferma inoltre che per la produzione di componenti automobilistici sono necessari 18 documenti chiave. Questi componenti devono essere messi a disposizione dei clienti dai fornitori o dai produttori. Il PPAP è essenziale per la produzione di nuovi pezzi, per le modifiche o le correzioni dimensionali dei prodotti, per le modifiche o le correzioni dei processi e per gli utensili inattivi da più di un anno. Il processo di approvazione dei pezzi di produzione, o PPAP, garantisce che ogni fase della produzione sia ben pianificata e presa in considerazione prima e durante la produzione. Può ridurre gli sprechi e gli errori inutili.