Экструзия силиконовой резины - один из самых распространенных процессов производства резиновых изделий. Этот метод широко используется на заводах с XVIII века. Экструзия силиконовой резины, как правило, формирует силикон и придает ему непрерывную длину.
Машина, используемая в этом процессе, называется экструдером. Она имеет центральную камеру, бункер и отверстие для фильеры. Сначала сырье поступает в бункер. Затем шнек в главной камере толкает его вперед. Там находится нагревательная камера, в которой силикон расплавляется или разглаживается. Расплавление силикона помогает создать форму в соответствии с формой штампа.
Этот метод позволяет получать гибкие, прочные и термостойкие силиконовые детали. Он прост, доступен и позволяет создавать идеальные силиконовые профили - экструзия становится все более распространенной.
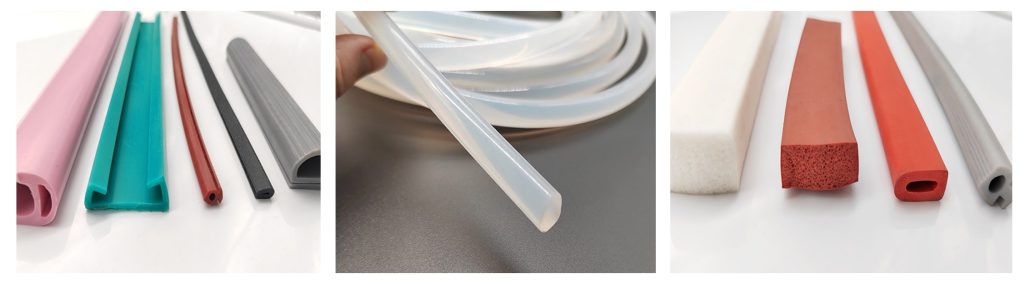
Экструдированные силиконовые изделия имеют множество применений. Одним из самых популярных продуктов являются силиконовые резиновые уплотнительные полоски. Этот продукт широко распространен для уплотнения машин, лодок и даже автомобилей. Другими продуктами являются силиконовые листы, трубки, и прокладки.
Эта статья в основном посвящена тому, как производятся эти экструдированные силиконовые изделия. Вы пройдете через все этапы, которые выполняются на заводах. Обратите внимание, что этот процесс может быть схож с другими видами резины.
Как изготавливаются силиконовые экструзионные профили?
Силикон - это очень гибкая, термостойкая и прочная резина. Одно из лучших качеств силикона - его термостойкость. Обычно он плавится при температуре от 80 до 220 градусов Цельсия. Поэтому вы можете понять, что процесс экструзии силиконовой резины должен быть способен выдержать эту температуру. Большинство производителей силиконовых экструдеров следуют нескольким этапам. Все эти шаги относятся к профессиональному уровню.
Шаг #1 Подготовка
Подготовка - первый важный шаг в процессе экструзии силикона. Ваша задача определяет, какое силиконовое вещество вы используете. При экструзии используются две формы силикона: твердый и жидкий. Людям нравится твердый силикон, потому что он долговечен и термоустойчив.
Далее следует проектирование экструзионной головки, которое также имеет огромное значение. Вы должны убедиться, что она изготовлена из отличной инструментальной стали и обладает высокой точностью. Обычно матрица формирует форму и размер готового экструдированного силиконового изделия. Чтобы изготовить новый продукт, необходимо сначала создать специальные фильеры.
Следующим важным моментом, который необходимо тщательно выполнить, является настройка экструзионного оборудования. Чтобы предотвратить загрязнение, необходимо очистить машины перед началом процесса. Также следует уделить внимание экспертной калибровке устройства. Как только все будет готово, можно приступать к процессу.
Этап #2 Смешивание и компаундирование материалов
Этап #1 также включает в себя этот этап. Мы включили его отдельно, так как он является одним из самых важных этапов процесса экструзии силикона.
Как вы знаете, экструдированные силиконовые профили бывают разных цветов. Кроме того, некоторые профили отличаются прочностью, а некоторые - высокой термостойкостью. На этом этапе вы можете определить, какое сырье необходимо использовать для получения этих свойств.
При изготовлении смеси можно использовать красители, стабилизаторы и антипирены. Красящие вещества обычно придают материалу внешний вид. Стабилизаторы повышают долговечность экструдированных силиконовых изделий. Однако антипирены имеют решающее значение для обеспечения безопасности во многих областях применения.
Весь этот процесс происходит в контролируемой среде. Некоторые называют это процессом измельчения, другие - процессом компаундирования. Независимо от названия, процесс включает в себя гомогенизацию силиконовой смеси.
Шаг #3 Настройка процесса экструзии силиконовой резины
После подготовки необходимо применить соответствующую настройку на производственной линии для экструзии силиконовой резины. Экструдер обычно состоит из нескольких компонентов: бункера, бочки и фильеры. Однако эти три компонента являются основными. Есть и другие важные детали.
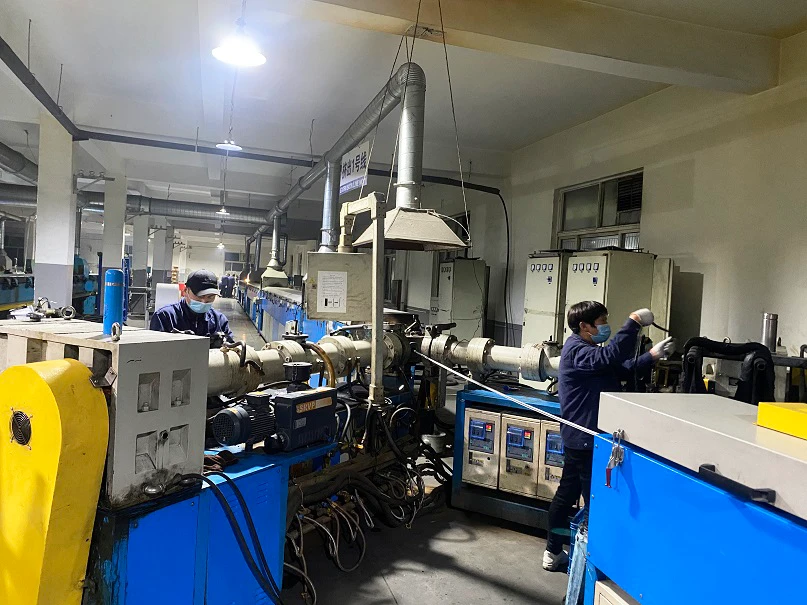
Когда вы помещаете сырой или компаундированный силикон в бункер, он попадает прямо в бочку. Внутри него шнек толкает их вперед.
Обратите внимание, что на каждом заводе процесс экструзии проходит в контролируемой среде. Одной из важнейших составляющих этого процесса является регулировка температуры. Поэтому необходимо проверять рабочую температуру. В то же время необходимо проверять давление. Наконец, можно отрегулировать скорость. Обратите внимание, что подходящая скорость зависит от толщины и формы профиля.
Обратите внимание, что необходимо правильно синхронизировать все вышеперечисленные факторы. В противном случае конечный продукт может не соответствовать дизайну. Поэтому на заводах специалисты всегда их уравновешивают. Как правило, это помогает им обеспечить качество экструдированных силиконовых профилей.
Шаг #4 Нагрев и экструзия силикона
Перейдем к самому процессу. Операция экструзии силиконовой резины может начаться, как только все будет готово. Сначала в бункер подается сырая или переработанная силиконовая резина. Постепенно бункер будет подавать их в экструдер, где имеется шнек. Шнек служит в первую очередь для продвижения материала.
В экструдерах обычно есть возможность регулировать нагрев. Температура должна быть достаточно высокой, чтобы расплавить силиконовый каучук. Почему необходимо плавить или смягчать силикон? Есть несколько причин. Главная из них заключается в том, что это помогает силикону плавно проходить через фильеру. Кроме того, силиконовый каучук необходимо постоянно нагревать, чтобы сохранить его свойства.
Шаг #5 Охлаждение и последующее отверждение
После того как силиконовая резина новой формы выходит из пресс-формы, ее необходимо охладить. Обратите внимание, что экструдированные силиконовые профили длинные и непрерывные. Поэтому холодильная камера должна быть достаточно длинной, чтобы охладить и затвердеть экструдированный силикон.
Существуют различные методы охлаждения. Процесс может осуществляться с помощью воздуха, воды или прохождения профиля по конвейеру. Независимо от способа, цель состоит в том, чтобы быстро стабилизировать форму.
Как мы уже говорили, существует множество изделий из силикона. Одни из них прочные, другие - гибкие. Опять же, одни могут выдерживать сильное нагревание, а другие - нет. Поэтому после охлаждения силиконовых экструзионных профилей им может потребоваться метод последующего отверждения.
Метод последующего отверждения обычно представляет собой процесс нагрева. В этом случае охлажденные профили дополнительно нагреваются для получения необходимых свойств. Обратите внимание, что этот процесс нагрева должен быть точным, иначе ваши профили могут оказаться бракованными. В целом, метод последующего отверждения повышает долговечность и прочность материала. Кроме того, он обеспечивает максимальную гибкость. Обратите внимание, что этот процесс повышает устойчивость силиконовых экструзионных профилей к высоким температурам.
Есть и еще одно преимущество метода последующего отверждения. В основном он снижает риск компрессионного схватывания. К сведению: компрессионный набор - это способность материала возвращаться к своей первоначальной форме после сжатия.
Если не проводить последующее отверждение, экструзионные изделия из силиконовой резины могут быстро износиться под давлением. Поэтому каждый завод обеспечивает надлежащий контроль как охлаждения, так и последующего отверждения.
Шаг #6 Резка и окончательная обработка
После охлаждения и последующего отверждения профили можно разрезать на отрезки различной длины или свернуть в рулоны для отправки оптом. Обычно эту работу выполняют станки, благодаря чему качество резки всегда остается неизменным.
После резки экструзионные профили из силиконовой резины могут нуждаться в дополнительной обработке. Такая обработка обычно улучшает внешний вид изделия. В основном используются такие методы, как обработка поверхности, обрезка и коэкструзия.
Обработка поверхности - это обработка поверхности материала. В случае экструзии силиконовой резины вы можете разгладить ее или нанести защитное покрытие. Обрезка, с другой стороны, позволяет отрезать лишнюю часть от профиля. Иногда также может потребоваться соэкструзия или мультиэкструзия. В основном они требуются для армированных или многослойных силиконовых профилей.
Шаг #7 Контроль качества
На этом этапе инженеры завода проверяют, соответствует ли продукт стандартам. На этом этапе могут использоваться различные методы проверки. Первый заключается в изучении размеров профиля. Второй - проверка поверхности на наличие трещин, пузырьков воздуха или неровностей. В-третьих, различные тесты проверяют растяжение и прочность профиля на разрыв. Проводятся и другие испытания, например, тесты на химическую защиту.
После тестирования фабрика обычно выдает сертификат качества, который впоследствии передается заказчику. При производстве соблюдаются некоторые стандарты, такие как FDA и ISO.
Шаг #8 Упаковка и распространение
Во время доставки клиенты обычно проверяют несколько вещей. В документе о транспортировке и соответствии перечислены отраслевые стандарты. Сертификаты качества свидетельствуют о том, что товар качественный. Качественная упаковка гарантирует безопасность перевозки, особенно при доставке за границу. Наконец, они проверяют количество доставленного товара.
Авторитетная фабрика, такая как Seashore Rubber, всегда гарантирует, что клиент выполнит эти требования. Они также обеспечивают точную и безопасную упаковку и распределение. Чтобы клиент мог понять, как правильно пользоваться изделием, ему предоставляются инструкции.
Экструзия силикона на заказ в Seashore Rubber
Экструзия кремния на заказ - это процесс изготовления уникальных профилей или конструкций. Другими словами, для изделий, изготовленных на заказ, не существует замены или стандартных фильер. Экструзия силиконовой резины на заказ становится все более популярной, поскольку потребность в уникальных инструментах резко возросла.
Экструзия силиконовой резины на заказ имеет ряд преимуществ. Во-первых, она позволяет удовлетворить разнообразные потребности клиентов. Во-вторых, она предлагает вам более точные решения и универсальность дизайна. Хотя первоначальные затраты могут быть выше, вы можете получить активный отклик на рынке.
В Seashore Rubber вы можете получить услуги по экструзии силикона на заказ. Компания предлагает высококачественные силиконовые профили для любой отрасли. Все, что вам нужно сделать для изготовления продукции на заказ, - это предоставить данные вашего проекта. Если ваш дизайн уже готов, вы сможете сэкономить время и средства. Можно также не иметь готового дизайна; инженеры компании могут создать индивидуальные штампы на основе ваших данных.
Свяжитесь с нами! Готовы начать свой проект? Связаться с компанией Seashore Rubber сегодня. Мы готовы помочь вам в решении ваших задач по экструзии силикона.