Die Produktqualität ist für jeden Hersteller der Schlüssel zum Erfolg im Wettbewerb. Daher konzentriert sich jeder Hersteller auf die Herstellung von Qualitätsprodukten und -dienstleistungen. Diejenigen Hersteller, die sich der Bedeutung dieses Aspekts nicht bewusst sind, sind auf dem Weg zum Erfolg verloren. Qualität ist eine der wichtigsten Eigenschaften für eine Marke, um den Markt zu dominieren, das Vertrauen der Kunden zu gewinnen und die Marke zuverlässiger als die Konkurrenz zu machen. Daher ist die Einhaltung von Qualitätsstandards für physische Produkte und Kundendienstleistungen der wichtigste Faktor für jeden Hersteller. In diesem Fall ist PPAP einer der wichtigsten Produktqualitätsstandards in den meisten Fertigungsindustrien.
In diesem Artikel wird das Verfahren zur Genehmigung von Produktionsteilen (PPAP) vorgestellt. Wir werden auch die Bedeutung des PPAP für die Leistung des Produkts auf dem Markt hervorheben. Außerdem wird auf die fünf PPAP-Stufen eingegangen, die in der Fertigung eine wichtige Rolle spielen. Am Ende dieses Artikels werden wir einige der wesentlichen Elemente des PPAP und die Unternehmen, die die PPAP-Standards anwenden, diskutieren.
Was ist der PPAP (Production Part Approval Process)?
Wie der Titel des Abschnitts bereits andeutet, steht PPAP für Production Part Approval Process, ein typisches Akronym für die Fertigung. PPAP ist der Schlüssel zur konsistenten Herstellung von Teilen und Komponenten in der Automobilindustrie. Er umfasst 18 Elemente. Dieser umfassende Prozess gewährleistet also die von den Verbrauchern erwartete hochwertige Produktion von Teilen und Ausrüstungen.
Der Ursprung des PPAP-Standards liegt in der Luft- und Raumfahrt- sowie der Automobilindustrie. Insbesondere in der AIAG (Automotive Industry Action Group). Später setzte sich diese Norm auch in allen anderen Fertigungsbetrieben durch, um die Produktionsqualität zu verbessern. PPAP unterstützt alle kritischen Aktivitäten in der Fertigungstechnik und erleichtert die Zusammenarbeit zwischen Lieferanten und Einkäufern. Dieser Prozess ist auch ein Teil von APQP. APQP steht für "Advanced Product Quality Planning".
Wenn ein Unternehmer eine Lieferkette im Zusammenhang mit der Automobilbranche initiiert, muss er PPAP durchführen. Neben der Automobilbranche wenden auch andere Industriezweige PPAP an, um technische Konstruktionen und Spezifikationen zu gewährleisten. In diesem Fall haben die verantwortlichen Unternehmen, FCA US, Ford Motors und General Motors, PPAP als kundenspezifische Anforderung oder CSR angegeben.
Die Bedeutung von PPAP
PPAP ist von entscheidender Bedeutung. Er stellt sicher, dass das für eine Automobil- oder Maschinenspezifikation benötigte Bauteil wie erwartet korrekt ist. Es bietet einen einfachen Leitfaden, der es den Zulieferern ermöglicht, die Kommunikation zu verbessern. Jeder Produktionslauf in einer Fabrik ermöglicht die Qualitätsausgabe und die Sicherung des Produktbedarfs durch PPAP. Dadurch werden die Risiken reduziert und die Umsetzung der richtigen Maßnahmen verbessert. PPAP macht den Herstellungsprozess reibungsloser. Die folgenden drei Punkte sind jedoch der Hauptzweck des PPAP.
- Sicherstellen, dass ein Lieferant die Qualitätsanforderungen des Kunden an sein Produkt einhält
- Nachweis, dass der Hersteller oder Lieferant alle Anforderungen der Produktspezifikationen und technischen Zeichnungen erfüllt hat
- Zur Überprüfung des genehmigten Herstellungsverfahrens
Was sind die fünf Stufen von PPAP?
Die fünf PPAP-Stufen sind so bekannt wie die fünf Teileinreichungsstufen. Diese fünf Teileinreichungsstufen sind entscheidend für den PPAP-Prozess, und ein Kunde sollte diese Dokumente von einem Verkäufer erhalten. In diesem Fall wird der Kunde, wenn er den PPAP benötigt, diese Teileinreichungsstufen befolgen.
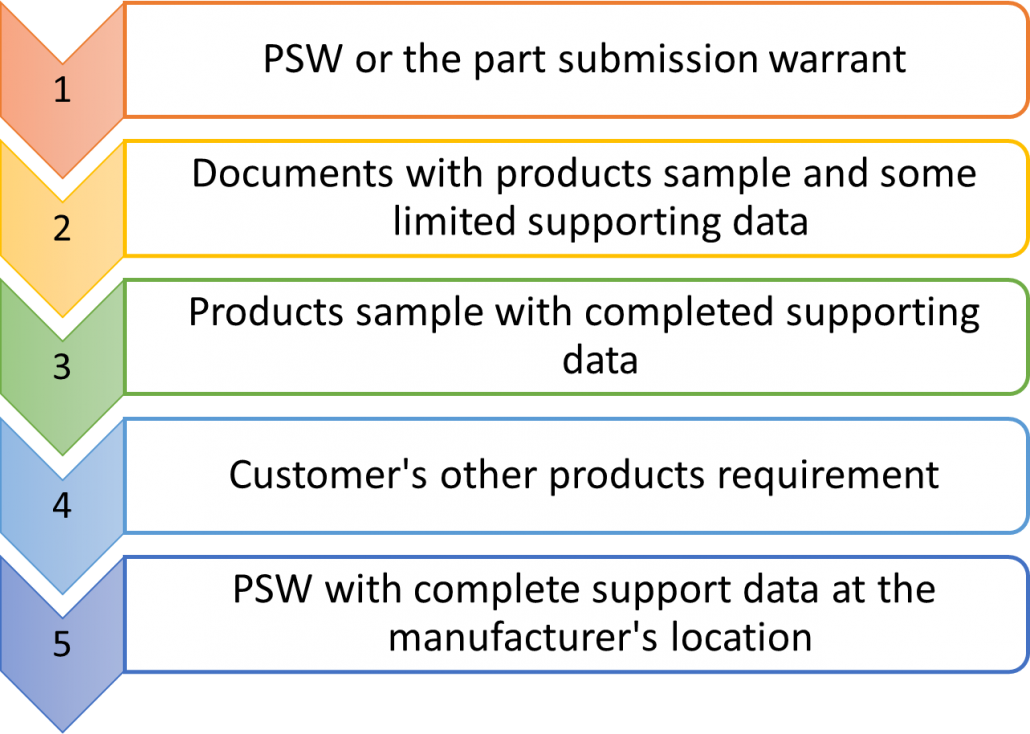
Nach Angaben der AIAG (Automotive Industry Action Group) muss ein Verkäufer die wesentlichen PPAP-Elemente eines hergestellten Teils berücksichtigen. Die Vorlage der erforderlichen Details hängt jedoch von dem Teil und den Anforderungen des Kaufauftrags ab. Diese fünf PPAP-Stufen geben an, welche Dokumente ein Lieferant dem Kunden aushändigen sollte.
- PSW oder der Teilvorlageberechtigung (Stufe 1)
- Dokumente mit Produktmustern und einigen begrenzten unterstützenden Daten (Stufe 2)
- Produktmuster mit ausgefüllten Begleitdaten (Stufe 3)
- Bedarf des Kunden an anderen Produkten (Ebene 4)
- PSW mit vollständigen Unterstützungsdaten am Standort des Herstellers. (Stufe 5)
Die PSW oder Teilevorlagegarantie ist Teil des PPAP-Prozesses. In der Regel weist der Lieferant damit nach, dass er die Anforderungen des Kunden erfüllen kann. Zu diesen Dokumenten gehören der Liefertermin, die Produktionsrate und die Produktqualität. Ein Lieferant muss alle diese Anwendungselemente sicherstellen. Andererseits sorgen die Qualitätskontrollen des PSW für die ordnungsgemäße Prüfung der Produkte.
Gemäß den oben genannten fünf PPAP-Stufen ist es wichtig zu beachten, dass diese Stufen im Ermessen des Käufers liegen. In diesem Fall muss genauer festgelegt werden, in welcher Situation welche PPAP-Stufe erforderlich ist. Daher muss jeder Zulieferer alle diese Angaben von den Herstellern aufbewahren.
Elemente des Genehmigungsverfahrens für Produktteile in der Fertigung
Die AIAG hat die PPAP-Checkliste ins Leben gerufen und kürzlich die Version 4 veröffentlicht. Nach der neuesten Version des PPAP-Handbuchs gibt es 18 Hauptdokumente, die für die Herstellung von Automobilteilen erforderlich sind. In diesem Abschnitt werden wir Ihnen diese 18 Elemente kurz vorstellen.
- Zu den Konstruktionsunterlagen gehören Zeichnungen von Kunden und Lieferanten, Materialzusammensetzungen und Bestellungen.
- Zu den Dokumenten für technische Änderungen gehören die Angaben zum Änderungsbedarf des Kunden und die ECN (Engineering Change Notice) der technischen Abteilung.
- Der Nachweis der technischen Genehmigung umfasst die von der technischen Abteilung genehmigten Musterprüfberichte.
- Design-FMEA: DFMEA oder Design Failure Mode and Effects Analysis umfasst Fehlermöglichkeiten und ihre Auswirkungen auf das Teil.
- Prozessflussdiagramme beschreiben den gesamten Prozess der Herstellung und Montage.
- Prozess-FMEA: PFMEA oder Prozess-Fehlermöglichkeits- und -Einfluss-Analyse umfasst alle möglichen Fehler in der Prozessqualität und ihre Auswirkungen auf die Endprodukte.
- Der Kontrollplan ist der nächste Schritt der PFMEA.
- Die MSA- oder Messsystemanalyse umfasst die Wiederholbarkeit und Reproduzierbarkeit von Messgeräten (GR&R).
- Die Dimensionsanalyse stellt die Daten dar, einschließlich der Toleranz und anderer Faktoren.
- Die Ergebnisse der Materialprüfung umfassen einen Plan und einen Bericht zur Entwurfsprüfung (Design Verification Plan and Report, DVP&R).
- Zu den ersten Prozessstudien gehört die statistische Prozesskontrolle (SPC).
- Die Dokumentation für qualifizierte Labortests umfasst die von jedem Qualitätsprüflabor genehmigten Zertifikate.
- Der Bericht über die Genehmigung des Erscheinungsbildes (AAR) enthält die Komponenten, die das Erscheinungsbild des Prüfteils beeinflussen.
- Produktbeispiel.
- Expertenmuster: Dieses Muster stammt in der Regel aus der Endprüfung und den Freigaben der technischen Abteilung des Herstellers.
- Zu den Kontrollhilfen gehören Werkzeuge zum Prüfen, Testen oder Messen von Teilen während des gesamten Montageprozesses.
- Berichte zur Genehmigung kundenspezifischer Anforderungen.
- PSW oder Teilvorlageberechtigung, einschließlich der fünf Vorlagestufen.
PPAP vs. APQP
Betrachten wir zunächst die Abkürzungen der beiden Begriffe. PPAP steht für Production Part Approval Process, und APQP steht für Advanced Production Quality Planning. PPAP befasst sich mit den Anforderungen an das Produktdesign und den vom Kunden geforderten Entwurf, Prozess und Design FMEAA, Prozessablaufplan, Kontrollplan, etc.
APQP hingegen befasst sich mit der gesamten Produktion und Prozessentwicklung. APQP hat fünf Gates, einschließlich der AIAG APQP-Anforderungen. Jedes Tor definiert die verschiedenen Dokumente und Anforderungen. Die fünf Phasen von APQP sind:
- Definition von Plan und Programm
- Überprüfung von Produktdesign und -entwicklung
- Überprüfung von Prozessdesign und Entwicklung
- Produktvalidierung und Feedback
- Einführung, Bewertung und Korrektur
Es ist wichtig zu beachten, dass der Prozess der Genehmigung von Produktionsteilen aus der APQP resultiert. Während der APQP-Prozesse werden die PPAP-Dokumente weiter geprüft. Die APQP-Phase befasst sich auch mit der technischen Überprüfung und der Genehmigung von Werkzeugen für Teile, die nicht im Werkzeugbau hergestellt werden.
Wer ist für PPAP verantwortlich, und wann ist es notwendig?
Die Zulieferer oder Hersteller sind für die PPAP-Elemente verantwortlich. Sie erstellen alle erforderlichen PPAP-Dokumente für jede Art von Produkt. Die Hersteller führen den Prozess in der Regel in enger Zusammenarbeit mit dem Qualitätsmanagementteam des OEMs durch.
Ein Genehmigungsverfahren für Produktionsteile ist erforderlich für die Produktion neuer Teile, für Änderungen oder Korrekturen der Produktabmessungen, für Prozessänderungen oder -korrekturen und für seit über einem Jahr inaktive Werkzeuge. In diesem Fall kann eine Produktänderung die Konstruktion, die Materialzusammensetzung, die Lieferung und die Funktion umfassen. Andererseits kann eine Prozessänderung aus einer Methode, Werkzeugen, einem Ort und Prüfkriterien bestehen.
Was ist die AIAG und was macht die AIAG?
Die AIAG (Automotive Industry Action Group) ist ein gemeinnütziger Wirtschaftsverband, dem die meisten Automobilhersteller, Zulieferer aller Größenordnungen, Automobilhersteller usw. angehören. Zu den AIAG-Mitgliedern gehören insbesondere Ford, General Motors, Toyota, Honda, Nissan, Caterpillar und mehr als 800 OEMs. PPAP ist jedoch eine der wertvollsten Normen, die von der AIAG entwickelt wurden.
Die Hauptaufgabe der AIAG besteht darin, ein offenes und neutrales Forum zur Erleichterung von Fertigungsmaßnahmen und gemeinsamen Problemen zu bieten. Ihr Ziel ist es, Standards und Richtlinien für Geschäftsprozesse zu entwickeln. Sie schult und trainiert Menschen durch Bewertungen, Veranstaltungen und Newsletter, um eine effizientere und verantwortungsvollere Lieferkette zu schaffen.
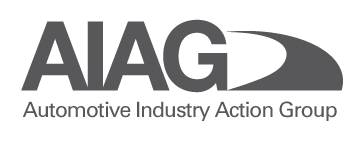
Schlussfolgerung
PPAP ist nicht nur für die Qualität des Produktionsprozesses notwendig, sondern auch für die Aufrechterhaltung einer hochwertigen Versorgung. Das Genehmigungsverfahren für Produktionsteile ist der Schlüssel zu den meisten Automobilindustrien. Auch die Herstellung von Dichtungsbändern erfordert PPAP, da es sich bei den Dichtungsbändern um Automobilteile handelt. Es gibt fünf PPAP-Stufen, bei denen der PSW oder die Teilevorlageberechtigung das wesentliche Element ist.
Im neuesten PPAP-Handbuch heißt es außerdem, dass für die Herstellung von Automobilteilen 18 Schlüsseldokumente erforderlich sind. Diese Komponenten müssen den Kunden von den Lieferanten oder Herstellern zur Verfügung gestellt werden. PPAP ist unverzichtbar für die Produktion neuer Teile, für Änderungen oder Korrekturen der Produktabmessungen, für Prozessänderungen oder -korrekturen und für Werkzeuge, die länger als ein Jahr inaktiv sind. Das Verfahren zur Genehmigung von Produktionsteilen (PPAP) stellt sicher, dass jeder Produktionsschritt vor und während der Fertigung gut geplant und vollständig berücksichtigt wird. Dadurch lassen sich unnötige Abfälle und Fehler vermeiden.